Porosity in Welding: Identifying Common Issues and Implementing Ideal Practices for Avoidance
Porosity in welding is a pervasive issue that frequently goes unnoticed until it causes significant problems with the integrity of welds. This usual flaw can jeopardize the strength and durability of bonded structures, positioning safety threats and causing expensive rework. By understanding the origin triggers of porosity and implementing reliable prevention approaches, welders can dramatically enhance the high quality and integrity of their welds. In this discussion, we will check out the key variables contributing to porosity development, examine its destructive impacts on weld efficiency, and go over the most effective techniques that can be adopted to decrease porosity incident in welding procedures.
Common Sources Of Porosity

Making use of filthy or wet filler products can introduce contaminations right into the weld, adding to porosity problems. To mitigate these usual causes of porosity, thorough cleansing of base metals, correct protecting gas selection, and adherence to optimum welding parameters are essential techniques in achieving top quality, porosity-free welds.
Influence of Porosity on Weld High Quality

The presence of porosity in welding can dramatically jeopardize the architectural integrity and mechanical properties of bonded joints. Porosity creates spaces within the weld steel, deteriorating its total toughness and load-bearing ability. These spaces function as anxiety concentration points, making the weld a lot more vulnerable to splitting and failing under used lots. Additionally, porosity can reduce the weld's resistance to rust and other ecological elements, even more reducing its durability and efficiency.
Welds with high porosity levels tend to exhibit reduced influence strength and decreased capability to flaw plastically prior to fracturing. Porosity can impede the weld's capability to successfully send pressures, leading to premature weld failure and possible security threats in crucial structures.
Finest Practices for Porosity Prevention
To improve the architectural honesty and top quality of bonded joints, what specific measures can be applied to lessen the occurrence of porosity throughout the welding procedure? Porosity avoidance in welding is crucial to ensure the honesty and stamina of the final weld. One reliable method is proper cleansing of the base metal, getting rid of any type of contaminants such as corrosion, oil, paint, or moisture that might result in gas entrapment. Ensuring that the welding devices remains in great problem, with tidy consumables and proper gas flow prices, can also substantially reduce porosity. Furthermore, preserving a stable arc and regulating the welding criteria, such as voltage, present, and travel rate, aids produce a constant weld pool that decreases the danger of gas entrapment. Utilizing the correct welding strategy for the certain material being bonded, such as changing the welding angle and gun placement, can additionally avoid porosity. Regular examination of welds and instant remediation of any kind of problems identified throughout the welding process are essential methods to stop porosity and generate high-grade welds.
Significance of Proper Welding Techniques
Executing appropriate welding methods is critical in making sure the architectural stability and quality of bonded joints, building upon the structure of effective porosity prevention measures. Too much warm can investigate this site lead to enhanced porosity due to the entrapment of gases in the weld pool. Additionally, using the appropriate welding parameters, such as voltage, present, and take a trip speed, is crucial for attaining audio welds with minimal porosity.
Moreover, the choice try this website of welding procedure, whether it be MIG, TIG, or stick welding, ought to align with the specific needs of the job to make sure ideal results. Correct cleaning and preparation of the base steel, in addition to picking the right filler material, are likewise important components of skillful welding methods. By adhering to these ideal practices, welders can reduce the danger of porosity development and produce premium, structurally audio welds.
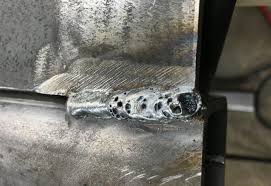
Checking and Quality Assurance Measures
Quality assurance procedures play a crucial duty in verifying the stability and dependability of bonded joints. Testing procedures are necessary to identify and prevent porosity in welding, guaranteeing the stamina and sturdiness of the last product. Non-destructive screening techniques such as ultrasonic screening, radiographic testing, and aesthetic assessment are commonly utilized to identify prospective issues like porosity. These strategies enable the assessment of weld quality without endangering the integrity of the joint. What is Porosity.
Conducting pre-weld and view it post-weld evaluations is likewise essential in keeping quality assurance standards. Pre-weld evaluations involve validating the materials, tools settings, and sanitation of the workplace to stop contamination. Post-weld assessments, on the other hand, analyze the final weld for any kind of problems, consisting of porosity, and confirm that it fulfills specified criteria. Executing a thorough high quality control plan that includes comprehensive testing treatments and inspections is paramount to reducing porosity concerns and making certain the total high quality of welded joints.
Conclusion
In final thought, porosity in welding can be a typical concern that impacts the quality of welds. By recognizing the typical reasons for porosity and carrying out best techniques for avoidance, such as correct welding techniques and testing measures, welders can make certain top quality and reliable welds. It is important to prioritize avoidance techniques to decrease the incident of porosity and preserve the stability of bonded structures.
Comments on “What is Porosity in Welding: Ideal Practices for Staying Clear Of Permeable Welds”